Sandvik Paint Plant - Conveyor
Sandvik Paint Plant Conveyor
For nearly 150 years, the name Sandvik has been synonymous with quality having annual sales of 89 Billion SEK and 47,000 employees worldwide. Sandvik’s Construction and Mining factory in Ballygawley, County Tyrone is now the centre of excellence for the manufacture of mobile crushing and screening equipment that are used within the mining and quarrying industries worldwide.
With the planned expansion of the current manufacturing facility at Ballygawley, Sandvik recognised that there was a requirement for a new finishing plant that would include shot blast booths, paint booths, ovens and an automated conveyor system in order to streamline this part of the production process and cope with the constant increasing demand of machines.
Working closely with the engineers at Sandvik and other associated major contractors, Amber Industries Ltd developed a turnkey solution and was subsequently awarded the contract for the new conveyor system utilising our standard Autotrack 500M Power & Free overhead conveyor.
The Requirements
The brief given by Sandvik was that the conveyor system had to handle all derivatives of crusher and screening components ranging up to 3000kg in weight and having a length of some 8000mm. A major requirement of the conveyor system had to be a means of easily loading and unloading of these long and heavy components and once safely loaded would be automatically transported through various items of plant and equipment, at times having to be stationary whilst in other areas of the process the product was continuously moving.
In order to achieve all of Sandvik’s requirements, the system was designed with 2 9000mm long drop sections, one sited at the loading area and one sited at the unload area. The load station having a stationary empty flight bar assembly in position that allows the operator to lower the flight bar down on the drop section carriage accommodating the conveyor track to an ergonomically suitable loading height.
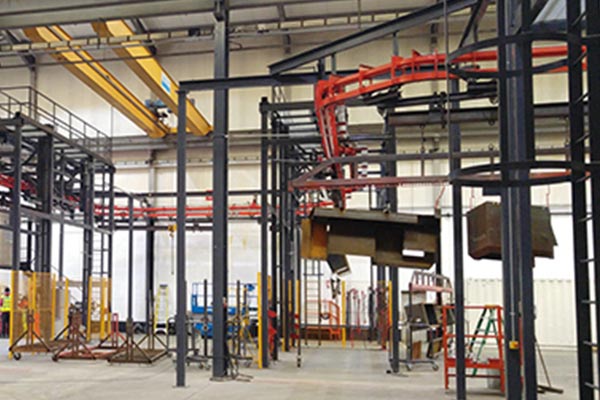
Flight bar and product are then transferred from the faster moving delivery chain onto a slower moving process chain where the product travels continuously at a given pitch through a primer booth and then through a green cure oven for a stipulated period of time and temperature.
After green cure and flash off, the top coat is then applied through a second powder coating booth which in turn travels through the main curing oven for final curing at a temperature of 220 degrees centigrade for a stipulated time period.
As part of the system the conveyor is fitted with a production stop facility that has a traffic light type signal that shows if the conveyor has been stopped for production purposes or as an emergency stop.
This facility allows operators to stop the process conveyor, whilst still allowing the delivery conveyor (fast chain) to continue to operate which in effect still maintains unloading operations without having to stop the whole of the plant.
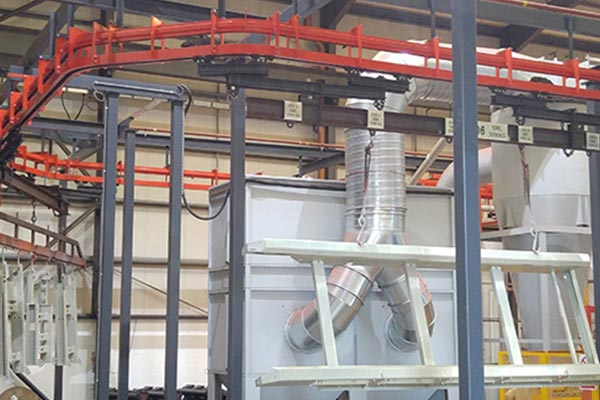
Unloading of product as with the loading is undertaken via a second 9000mm long drop section allowing operators to lower the stationary finished painted product down to a suitable unload height, upon removal of product the empty flight bar rises back to high level and is transported back to the load drop section, check gates are fitted at the drop sections to ensure safe removal of product, Major benefits of the drop sections ensured that lowering of the product could be achieved within a small area compared to that of a conventional conveyor rise and fall. The fact that the stationary flight bar can be lowered down to suitable load and unload heights are found to be beneficial to operatives as this accommodates for the various sizes of products to be handled.
Using state of the art electronics enables the integration of the conveyor system to work in conjunction with other plant and equipment ensuring correct product movement and timings as and when required. The master control is installed with a remote access facility allowing Amber Industries ltd software engineers to access the system from our manufacturing facility at Oldham, Lancashire.
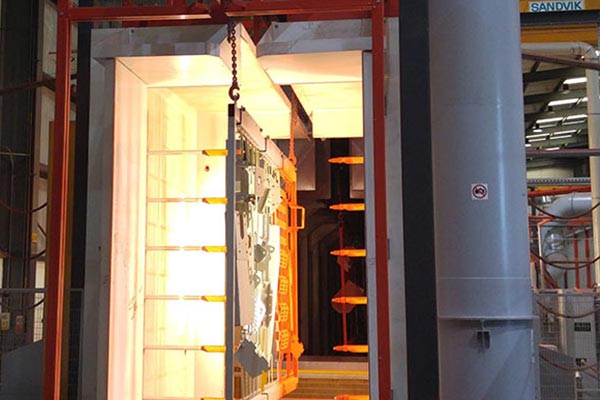