Amber Automation Powered & Gravity Roller Conveyor Systems
Roller conveyors make up the main part of many automated floor conveyor systems. They consist of a series of rollers over which objects are moved and they can be designed and manufactured for a great many applications at relatively low cost.
Amber Automation offers a wide range of roller conveyors including simple gravity (free roller) conveyors, lineshaft and motorised roller (zero line pressure) powered roller conveyors and chain driven live roller conveyors. All our roller conveyors come in a selection of widths, roller diameters, roller pitches and transit speeds so that they can be matched to specific load and throughput requirements.
Gravity Roller Conveyors
Gravity roller conveyors are a simple low cost and ergonomic way to move materials.
They move product loads without utilising a motor to provide the motive power, usually down an incline or by means of a person(s) pushing the product load along a flat conveyor.
End stops may be supplied to stop loads falling off the end and the speed that loads accelerate down a slope can be controlled by the incorporation of centrifugal force activated brake rollers.
Amber Automation’s gravity conveyors can be fitted with a choice of zinc plated or PVC rollers.
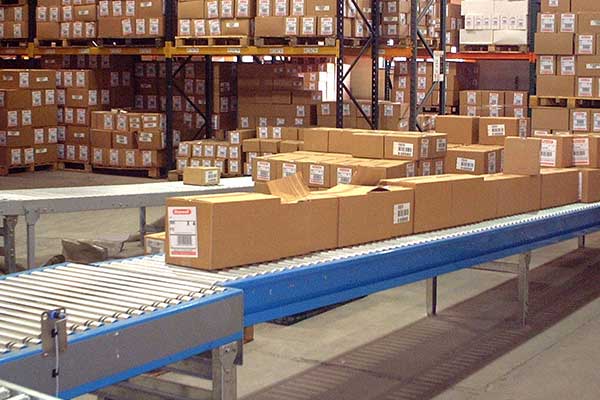
Lineshaft Powered Roller Conveyor Systems
Lineshaft roller conveyors are powered by a shaft running longitudinally beneath the rollers to which are attached a series of spools. Polyurethane O-rings run from each spool around a groove in the rollers, thus as the shaft is rotated by an electric motor the rollers also rotate in turn pushing the product along the conveyor.
Lineshaft roller conveyors are ideal for transporting light to medium products that are regular in shape and size, fairly rigid with an even underside e.g. boxes, cartons, totes, platens etc.
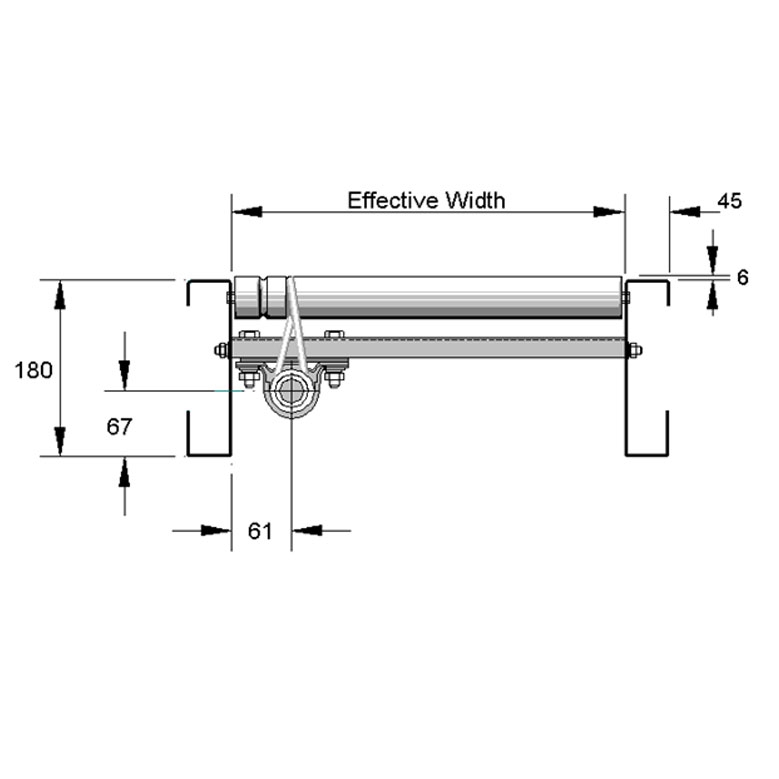
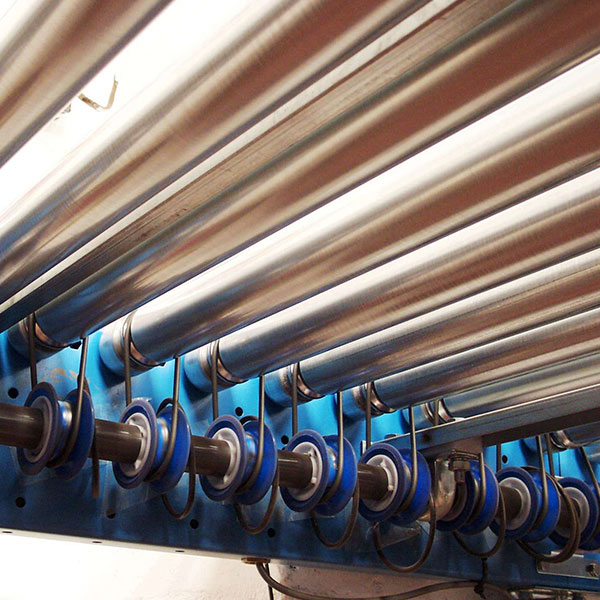
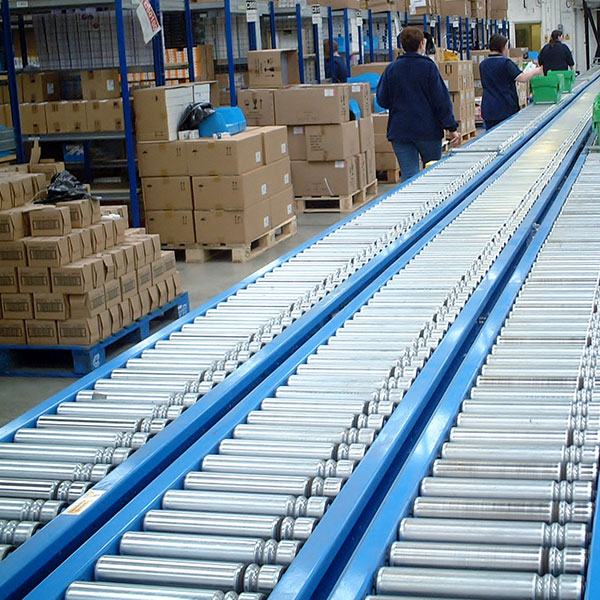
Products can be accumulated on lineshaft conveyors, i.e. a queue of items can be allowed to form to create an in-line buffer store without stopping the upstream movement of products on the conveyor system. This is possible because a property of the lineshaft drive mechanism design is that it only generates low levels of line pressure. This is the amount of force acting between touching products in the queue. When products are stopped on the conveyor by a mechanical stop, the friction between the product and the rollers beneath then causes the rollers to stop rotating and the corresponding O-rings to slip on their spools, without affecting any other rollers elsewhere on the conveyor.
Lineshaft Modular Design
The Amber Automation range of lineshaft conveyor equipment is of a modular design making it easy to configure systems of any layout and make modifications/additions at a later time.
It is quiet in its operation and robust in its construction.
It has a neat and sleek appearance due to the folded channel (180mm deep x 45mm wide) side-frame construction being free from bolt heads or other protrusions and fitted with a side covers which form an enclosed box section into which services such as cables and airlines etc. can be put out of sight.
Drive units are fully guarded and intrinsically safe.
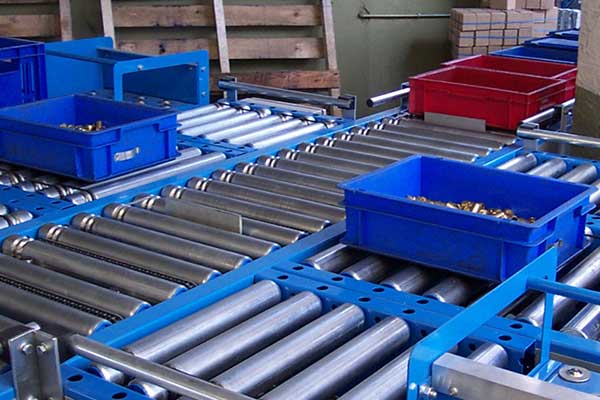
Standard Module Lengths, Conveyor Widths, Roller Pitches, Curve Angles Are Available as Follows
The design of Amber Automations lineshaft conveyors enables rollers to continue to be powered on curves, spurs and transfers from just a single drive motor. Not only does this minimise the number of relatively expensive electric motors required but it reduces the time and cost of installation.
- Conveyor Widths (b/n sideframes): 300mm, 400mm, 500mm, 600mm, 800mm & 1000mm
- Straight Module Lengths: 500mm, 1000mm, 1500mm, 2000mm, 2500mm & 3000mm
- Curve angles incorporating tapered rollers: 30°, 45°, 60° & 90°
- Roller pitches: 62.5mm, 83mm, 125mm & 167mm
A comprehensive range of ancillary equipment is also manufactured in-house to go with our lineshaft conveyors e.g. leg stands, end plate stops, tapered roller curves, transfers, corner turns, merges and switches, blade stops, chain transfers, pack turn and positioning units, diverts, pushers and personnel lift gates to name a few; indeed we are able to supply everything necessary to provide a complete fully functioning conveyor system.
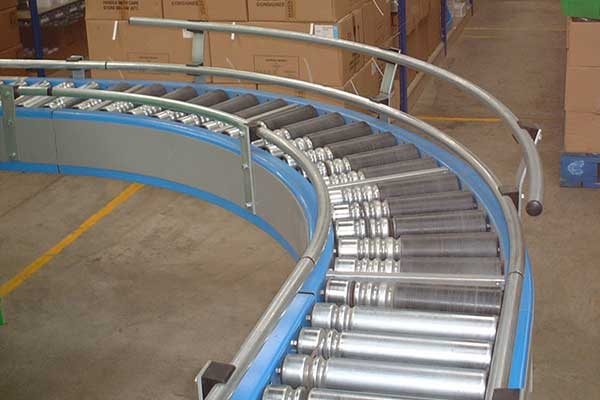
Zero Line Pressure (Motorised Roller) Conveyor Systems
Zero Line Pressure (ZLP) conveyors allow products to accumulate without contact so there isn’t any build up of line pressure between adjacent products in a queue.
This makes them ideally suited for conveying fragile or sterile products where gentle handling is required and/or where there is a requirement to release single products from the queue at set intervals.
Amber Automation’s Zero Line Pressure (ZLP) conveyors are set up with a series of ‘product zones’ along the accumulating section of the conveyor system.
These zones, which can be 500mm, 625mm, 750mm or 1000mm long to suit product size, are individually controlled by means of a photoelectric cell positioned in the zone and driven by a 24vdc motorised roller connected to the slave rollers within its zone by elastomeric urethane belts.
The rollers in any one zone or selected zones can therefore be feeding product whilst other zones remain stationary.
Our ZLP conveyors allow accumulation of product on curves and on inclines and declines which gives them a greater capacity for accumulation over other types of conveyor.
Amber Automation’s ZLP range is modular in design, safe and quiet in its operation, robustly built, aesthetically pleasing and incorporates cable containment.
It is straight forward to assemble and easy to wire up.
It is available in a range of lengths, widths, and roller pitches and the full range of ancillary equipment can be supplied to provide a turnkey conveyor solution.
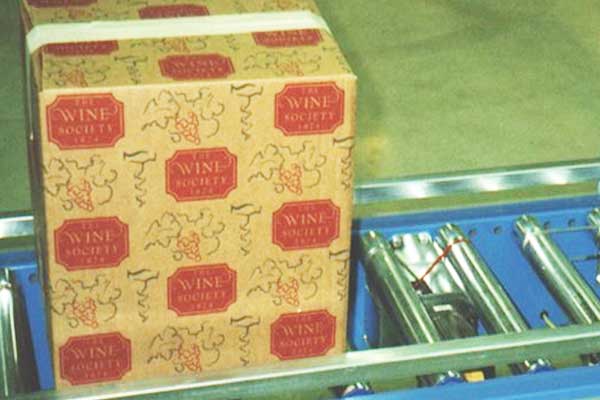
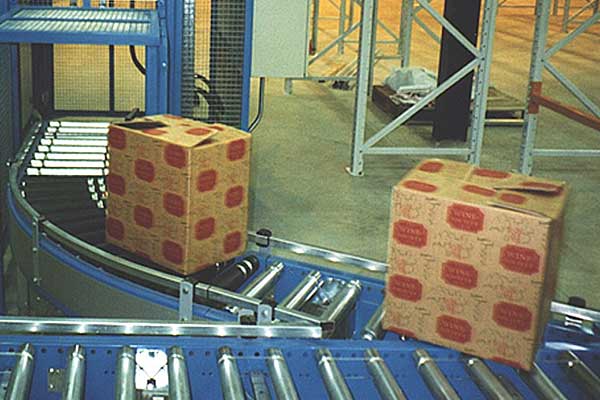
How ZLP Conveyors Work
The typical sequence of operation of a ZLP accumulating conveyor is as follows: once the photoelectric cell in a downstream zone signals that zone to be vacant the onboard ASI control system tells the next zone upstream (if occupied) to power up and feed its product forward. Once the product has cleared this second zone its photoelectric cell signals it to be vacant whilst the photoelectric cell in the first zone is now signalling ‘zone occupied’. The control system now tells the third zone (if occupied) to power up and feed its product forward, and so on feeding products along the accumulating conveyors zones in a cascading/indexing manner.
The rollers in any one zone of a ZLP conveyor only power up if there is product to be fed forward and if there is no product available at all then all zones are stopped. This means that unlike most other types of conveyor system ZLP only uses electrical power when needed to move product thus making it relatively energy efficient.
Positive dynamic braking of the motorised rollers ensures accurate stopping and positioning of the product in each zone and a built in shock absorber in the motorised rollers protects the roller from being damages by sharp deceleration of product.