Laundry Conveyors
Commercial laundries typically process over 500,000 items of loose linen per week and to do this efficiently automation is essential. Conveyors form the backbone of automated transport systems within laundries, moving the separate items of linen between the dirty linen receiving areas, through the laundry cleaning processes and on to packing and final dispatch of items back to the user.
Typical conveyor applications within laundries include;
- Dirty linen sorting
- Indexing step conveyors to load CBW washers with 50-100Kg loads
- Cake conveyors
- Linen sorting belts and platforms
- Dryer loading shuttle cars and takeaway conveyors
- Shrink wrapper infeed and outfeed belts
Many laundries operate on mature sites with many items of legacy equipment in place and a challenge for automation is finding space to install conveyors. All Amber conveyors are designed and built for the individual application and so are easily tailored to suit the site requirements by altering the length, width and height of belt.
- Powder coated, mild steel, beds with stainless steel or powder coated valances
- Smooth internal surfaces
- Gap free internal surfaces
- Hemmed edges around valances
- Continuous belts
- Finger nip guards located on crown of roller and robust
- Horizontal conveyors preferred immediately before drop transfer positions
- Increase conveyor speed when transferring from one belt to another
- No loading above sides of valances
- Drop heights between conveyors to be no less than height of valance of the feed conveyor
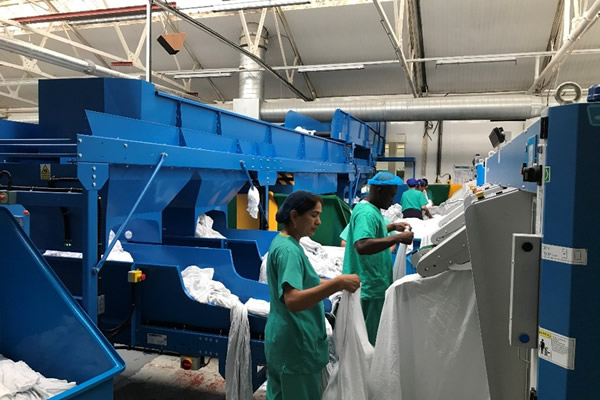
Applications For Conveyors In Laundries
Commercial laundries typically process over 500,000 items of loose linen per week and to do this efficiently automation is essential. Conveyors form the backbone of automated transport systems within laundries, moving the separate items of linen between the dirty linen goods inwards areas, through the laundry processes and on to packing and final dispatch of cleaned items back to the user.
Goods inwards will use belt conveyors to quickly move dirty linen from the delivery lorries to the sorting or washing areas. Sorting may also take place on the goods inwards conveyors depending on the laundry layout. After washing, the clean linen may be pressed into a “cake” to remove excess water and conveyors will be used again to transfer the cake to a sorting area or direct to dryer machines. After drying more conveyors are used to transfer the linen prior to teams of operators who will feed banks of ironers and folders.
Once ironed and folded the linen may travel on one final conveyor that leads to the dispatch department where it will be stored ready for return to the user. To improve the efficiency of the laundry conveyors other items of material handling equipment are often used including lifts, hoists and shuttle cars. The laundry process may run for over 120 hours each week, 52 weeks a year and so reliable, robust and resilient equipment is necessary at every stage and this is where the Amber laundry conveyors excel because of their laundry specific designs.
Many laundries operate on mature sites with lots of legacy equipment in place and a challenge for automation is finding space to install conveyors. All Amber conveyors are designed and built for the individual application and so are easily tailored to suit the site requirements by altering the length, width, and height of belt.
The loose linen processed with laundries poses a unique set of challenges for automation and in particular for conveyors which may be combated by good design. Snagging of linen along a conveyor is the biggest potential issue and must be countered by ensuring that the internal surfaces are smooth, continuous and wherever possible gap-free. Gaps that taper down in the direction of travel are to be avoided at all costs because line is sure to snag in the gap and become firmly wedged.
Linen transfer around a laundry is usually accomplished using a series of linked conveyors and where the conveyors meet is a potential snag/trap point for linen as it rolls away from one conveyor to be collected by the other. To reduce the possibility of linen trapping at the junction between conveyors the speed of the takeaway conveyor should be measurable greater than the feed conveyor. This speed differential is particularly important on conveyors which change orientation from declined to horizontal where there is a tendency to drive the linen into the gap between the rollers.
The use of small diameter rollers e.g. 60mm diameter at the head and tail of conveyors is beneficial to reduce the size of the “vee” gap between the rollers and so reduce the gap that the linen must jump when transferring from one conveyor to another. Tuck-under, where linen sticks to the conveyor belt and starts to follow the return belt path beneath the conveyor can occasionally be a problem and is best countered by reducing where possible the friction of the belt so linen peels away easily or in situation where this is impossible by adding a sensor below the head roller that’s linked to the E-stop of the conveyor to stop the conveyor as soon as a piece of linen attempts to move along the return belt.
Safety is of paramount importance and often requires the use of nip guards at the head of conveyors. These nip guards can be the cause many linen snags and jams unless correctly designed by placing them as near to the crown of the roller as possible and ensuring that they are rugged to withstand the rigors of the occasional, inevitable, jam and subsequence clearance. Where a powered conveyor discharges onto a stationary or slow moving surface like a table or a gravity roller then nip guards are usually unsuitable and should be replaced by other safety systems such as electrical bump strips linked to the emergency stop circuit of the conveyor.
Protection on the underside of the conveyor for the return belt can be achieved using full panel underguards or local roller covers and both provide acceptable levels of safety. For conveyors below 750mm from the ground roller covers are often the preferred option because they are an economic solution, they allow lint and other debris to drop to the floor for easy clean-up and the likelihood of operators touching the moving belt is remote. Conveyors between 750mm and 2500mm from the floor are often fitted with full underguards, mainly because, psychologically, operators dislike being next to a moving belt – even when the trap points (return rollers) are adequately guarded using covers.
At belt heights greater than 2500mm roller covers are almost always used because operator contact with the moving belt is unlikely and cost becomes the overriding factor. Also, the roller covers allow maintenance staff to easily monitor the belt condition because most of the belt is exposed to view.