SEW Eurodrive - Overhead Conveyor
Automated Conveyor System for SEW Eurodrive
SEW Eurodrive are globally recognised as market leaders in drive engineering stretching across five continents and employing 14000 people. When their new manufacturing facility at Normanton, West Yorkshire was in the planning, SEW recognised this as an opportunity to introduce an automated conveyor system to service the new paint plant facility that would streamline the existing process for their range of drive equipment.
Working closely with the engineers at SEW Eurodrive, Amber Industries Ltd developed a turnkey solution and was subsequently awarded the contract for the new conveyor system utilising our standard Autotrack 500M Power & Free overhead conveyor.
The brief given by Sew Eurodrive was that the conveyor had to handle all derivatives of geared motor units ranging from 15kg to 1000kg, These units being loaded at one end of the factory and the system to have the ability for diverting product from daily business and coloured lanes together with a "Fast-Track lane". The fast track lane that by passes normal daily business is very important to SEW as they pride themselves upon their service of having the ability to deliver to customers on an urgent basis.
There was also the requirement of the conveyor having the capability of raising and lowering product within the spray booth and at the inspection area whilst allowing the operator to rotate the unit during the spray process. A multi height drop section at the inspection area allowed the operator to inspect the product thoroughly prior to despatching to the appropriate unload stations.
In order to achieve all of SEW requirements, the system was designed with 2 loading stations having a stationary trolley set assembly in position that would allow the operator to attach the product onto the trolley load bar support points, smaller products being suspended from any of the rotation units on the load bar, whilst larger product would be suspended from the central rotation point.
The operator at either of the two load stations scans the product(s) and then presses a button at his work station that determines if the loaded trolley is to be routed to normal business, colour or Fast Track.
When the trolley arrives at the storage lanes, the conveyor switch point automatically diverts the trolley into the appropriate storage lane.
A monitor within the spray booth allows the operator to view the jobs in hand, allowing him to select from the appropriate lane. The Fast Track lane can by-pass accumulating daily business enabling the unit to be painted without being held up by normal business.
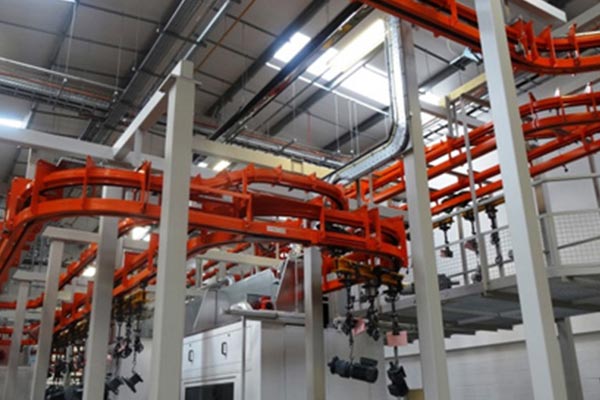
With the trolley now in the spray booth, the operator can lower the drop section as required to an ergonomic height due to the differences in product size to allow him to spray all the relevant aspects of the product whilst remaining stationary.
The load bar assembly was designed such that the products can be turned through 360 degree during the spraying operation and then locked after the spray operation to maintain correct product orientation. A major benefit of the drop section ensured that lowering of the product could be achieved within a small area compared to that of a conventional conveyor rise and fall.
With the paint spray process now complete and the drop section in the raised and locked position, the operator again presses a button that determines once more if the product routing is that of standard daily business or if the trolley route is that of "fast track".
The trolley set that now contains the painted product would automatically be released back into the system where it will dry in the Drying Oven for a stipulated time period and temperature. Products are then automatically accumulated and released out of the dryer once they have been in the oven for the allocated time.
As the overall paint plant facility has automatic opening doors within certain parts of the plant, the electronic controls on the conveyor system have to be synchronised with these elements to avoid clash conditions when opening and closing.
Product then gets routed to the main dry off oven where again they are accumulated within the oven for another differing stipulated time and temperature.
Upon exit of the main curing, the trolley set complete with dried product would then be automatically diverted either into the normal business line or routed to the "fast track" lane.
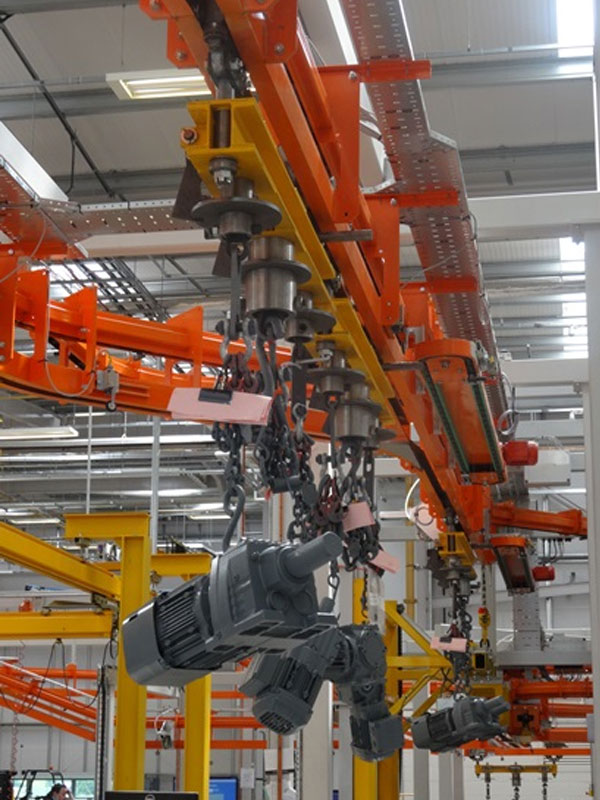
Products that are deemed for daily business would be diverted into a storage loop which in turn then continues to travel to the multi height inspection drop section, but trolley sets that are deemed as Fast Track (urgent orders) do not enter the normal business loop, these are diverted directly to the inspection drop section. The loaded trolley set is again stationary for the inspection process allowing the operator to raise and lower the product together with rotation through 360 degree for full inspection.
Upon completion of inspection the operator determines if the product is to be transported to unload station 1 or 2. And the inspected unit is now automatically routed to the pre-requisite unload destination. After unloading, the empty trolley sets are routed back to the loading stations. Using state of the art electronics enables the integration of the conveyor system to work in conjunction with other plant and equipment ensuring correct product movement and timings as and when required. Consideration also had to be given to where products passed over gangways, with this in mind and the weights involved, a heavy duty walkable underside guarding was provided where necessary.